面對越來越多元化、高標準的消費者需求,汽車制造企業一直致力于科技創新和標準升級。人工智能、虛擬仿真、邊緣計算、物聯網……在這滿滿的“黑科技”背后,是對品質的永恒追求。一直以來,領克汽車圍繞高質量發展理念,不斷應用創新科技來激活生產潛力和完善質量體系。通過吉利工業互聯網平臺的賦能,領克在智能制造領域又一次實現突破,打造出一座高效率、高質量、節能環保數字化工廠。
位于成都的領克工廠總占地面積1444畝,是全球最先進的汽車生產基地之一。擁有完善的IT系統、先進的信息管理模式、一流的高精尖設備、全球統一的嚴苛豪華品牌制造標準等,實現了高度智能化、無人化、定制化生產,工廠年產能可達30萬臺。
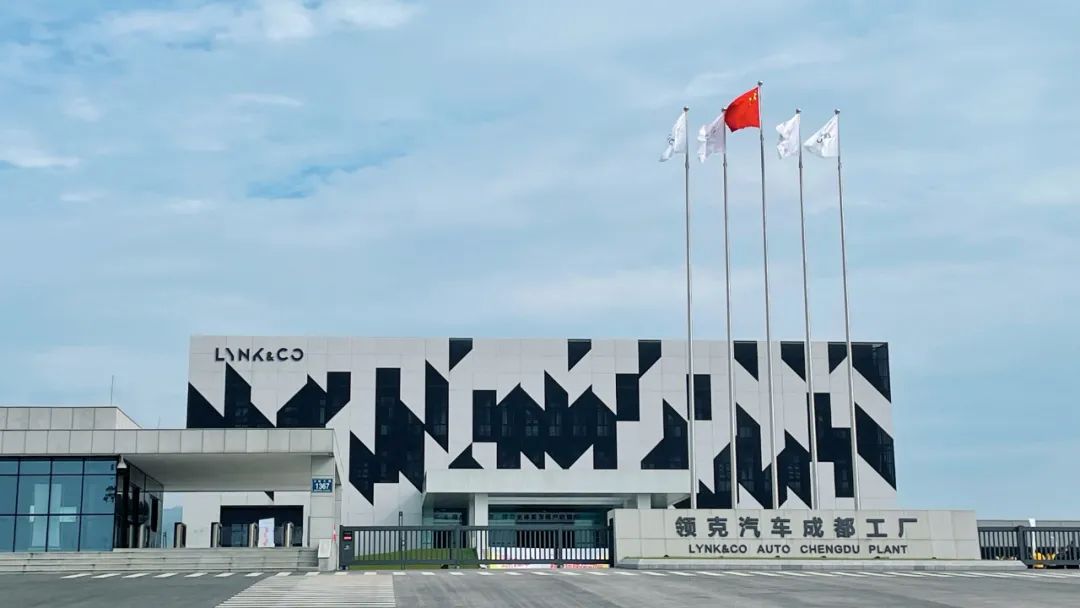
在這座大型工廠里,廣域銘島吉利工業互聯網平臺的智能化產品遍布沖壓、焊裝、涂裝、總裝等各大車間,為工廠構筑了堅實的數字化基礎。今天,小編就帶大家深入領克工廠內部,從源頭揭秘數字技術在真實場景中的落地應用,近距離感受“智造”黑科技的魅力。
Geega工業物聯網平臺不同于市面其他IIoT平臺,其核心不止連接,更多的是為機理模型全生命周期提供服務,融合OT與IT,構建模型開發、訓練、驗證、迭代的全流程體系,幫助企業實現數字化業務的持續優化與提升。
IIoT平臺作為領克工廠數字化轉型的基石,通過連接、鏡像、融合、協同等特性支撐上層工業軟件應用,提供即插即用的設備連接能力、數字孿生鏡像能力以及產品全生命周期服務能力, 打破傳統煙囪式軟件架構體系, 使制造基地與供應鏈之間形成產業協同。
沖壓智能排產:以沖壓智能排產系統替代了傳統的人工手動排產,擔當生產調度的智腦。基于沖壓排產機理模型,結合有限產能約束、DBR瓶頸、啟發式算法等理論與技術,實現一鍵排產。
模具智能維保:自動采集沖次記錄,并根據各保養類型的參數配置自動觸發保養工單,并及時發現生產中的異常情況,自動派發維修工單。且與排產系統協同,將模具維修工單的處理與排產計劃相聯動。
容器智能管理:通過RFID技術可實時掌握容器狀態,為排產系統提供數據輸入,支持車間排產單批次零件生產數量達到最優,防止問題容器長期閑置。
焊接質量管理:通過焊點質量管理系統,實時獲取生產過程中的海量焊點數據,基于焊接過程電熱平衡和焊接參數模型應用,對每一個焊點進行質量統計與分析,對生產過程中的缺陷焊點實時預警。
焊接尺寸管理:通過尺寸管理系統整合焊裝設備在線測量、藍光測量、三坐標測量、DTS測量、內間隙測量的五維數據,基于公差傳導模型,結合算法與大數據,分析尺寸失效原因。
色差管理系統:色差管理系統通過色差識別、色差預警、色差預測、色差目視評審等內容,對色差管理實現自動化、智能化、透明化和精準化,為涂裝漆面外觀管理提供數據支持,提升涂裝外觀管理質量。
缺陷識別與根因分析:利用工業視覺技術自動識別缺陷位置及類型,高效精準;結合NLP技術與聯邦學習技術構建知識圖譜,自動進行缺陷分析,指導工程師進行缺陷整改并沉淀為知識庫,最終實現缺陷預測和規避。
對領克工廠制造全流程碳排放進行識別、監測、采集,實現企業碳盤查;建立汽車制造全生命周期碳排放評價模型和核算方法,通過碳足跡可信數字化,初步實現領克工廠的汽車碳足跡標識。
同時,針對鍋爐、空壓機、制冷機、循環水等共用動力版塊,以IIoT平臺為依托,通過機理模型、人工智能、自動控制等技術,實現能源的精準供應以降低能源成本。
OWL通過融合生產拉動、倉儲、物流各自的業務特點,實現車間物料資源的柔性配送,構建生產與車間物流的一體化價值鏈,全面提升了工廠的執行效率和空間利用率,降低了運營成本。
倉儲物流規劃系統(OPS):根據生產規劃、零配件數據、場地大小等,自動輸出倉儲物流規劃方案,根據料件及節拍變化,實時優化倉儲布局,動態調整物流路線。
全面倉儲管理系統(OWS):將料架、容器、貨物智能化,通過數字孿生,實現能力透明化,與立庫、線邊倉等全面打通,實現按需存儲、動態儲位等倉儲服務。
全域物流調度系統(OLS):根據生產指令與計劃,實現運輸調度、搬運、分揀的無人參與和自動化,通過大量AGV機器人全面提高搬運效率,降低成本。
目前,工廠數字化解決方案除了在領克工廠實施,亦落地在湘潭基地、極氪工廠、百礦鋁產業基地中,未來還將在極星基地、晉中基地、梅山基地等更多實際場景進行充分應用和驗證。廣域銘島要做的是深入每個工業場景中,去發現問題、解決問題,讓數據產生落地價值,真正為企業數字化轉型提供動力。